CMMS saves time by automating work orders, maintenance schedules, inspections, and data collections but when it comes to having real-time access to mission-critical information, you need a mobile CMMS application. While computerized maintenance management systems make your job a whole lot easier, the mobile ability of CMMS boosts both productivity and performance. If you are still wondering why you should go mobile with your CMMS, here are 5 solid reasons that will surely turn your contemplation into a sound choice. Let’s see some benefits of mobile cmms
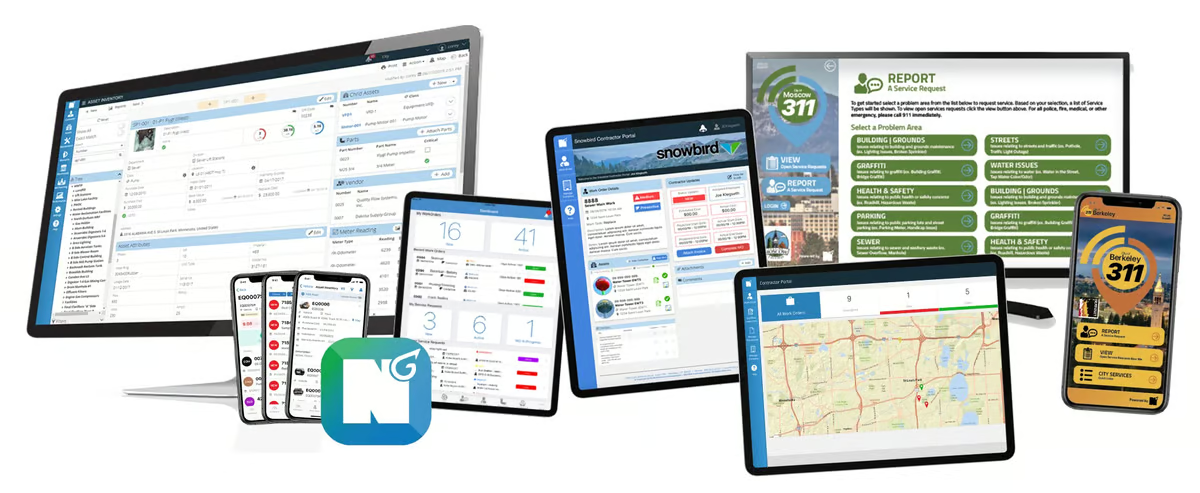
First Learn How CMMS Works.
If you’re looking for a way to make maintenance easier, CMMS software might be just what you need.
Learn About What is CMMS
What Are the Benefits of Mobile CMMS?
-
Accelerates Workflow
Work orders drive maintenance departments and as your maintenance crew is out in the field for most of the time, they need instant access to asset data and work orders from the CMMS. With a mobile CMMS in place, facility managers can dispatch work orders in real time and send notifications to field technicians instantly. Handheld devices enable field technicians to search work orders by equipment, enter the maintenance time taken on the field, close orders on completion and enter the next work order to keep the facility managers updated on work progress. Using mobile CMMS saves travel time, improves response time for on-demand tasks, and increases job satisfaction while keeping labor costs in line.
-
Facilitates Instant Communication from any Location
If a vital component breaks down, a technician must fix it immediately and make the necessary repairs with minimal disruption in the flow of maintenance schedules. To avoid such unexpected failures and avoid major expenses, technicians must be able to respond in real-time. Mobile CMMS brings the ability to stay flexible and adaptable by sending an instant notification when breakdowns occur along with a complete record of repairs and maintenance performed previously. With real-time visibility of serviceability and equipment conditions, facility managers can also prevent workplace hazards and ensure a safer work environment.
-
Reduces Downtime
Manufacturing facilities, oil rigs and power plants involve productive assets and if these assets experience loss of capacity or downtime during maintenance, the break-fix scenario should not take long. Returning any asset to productive use in a timely and efficient manner requires speedy communication. Mobile CMMS notifies the technician on the go, eliminating the need to report to the central office and check the scheduling board. It dramatically reduces downtime by keeping technicians updated on which parts need urgent replacements, which parts are currently available, and which equipment would require a repair service sometime soon. This improves work efficiency and gets the machine back to peak efficiency promptly. When managing multi-faceted assets with several dependencies, downtime affects all concurrent activities. With Mobile CMMS, facility managers can prevent surprise downtimes and minimize the impact of planned downtime by recording work in real-time, making revisions immediately, and routing information to field technicians on the spot.
-
Optimizes Parts Integrity Management and Improves Control over Assets
Managing maintenance inventory in a facility that houses hundreds of equipment can get tedious and time-consuming. When CMMS is integrated with mobile technology, facility managers have all the information about replacement parts at their fingertips. Adding RFID functions and Bar codes ensures complete inventory accuracy and makes it much easier to manage cycle counts and reorder levels. When maintenance technicians have maintenance inventory and other important data at hand on site, problems are alleviated before they turn into emergencies. Mobile technology adds value to assets by regularizing scheduled maintenance, improving the productive capacity of assets and enhancing their readiness and serviceability.
-
Reduces Paperwork and Saves Time
Using mobile CMMS saves tremendous time and human effort by allowing technicians to work on the go. Since the work orders are sent out on the spot, technicians don’t need to report to the office and collect paperwork orders. Even when the job is done, all the updates can be sent to the facility manager from the field. With real-time access to information, workers get all the information on time at any location without wasting any time on the paperwork that can get lost or misplaced. A mobile CMMS keeps all the notes and information handy and is far more efficient in sustaining a paperless environment.
-
Boost Productivity
80% of maintenance technicians spend an average of 30 minutes every day just retrieving information. Mobile CMMS offers an end-to-end view of asset operations and maintenance schedules across departments enabling maintenance technicians to save tremendous time and effort when tracking inventory levels and searching for spare parts. Maintenance managers on the other hand have real-time insights into the hours spent on resolving maintenance issues which in turn increases transparency and improves accountability thereby accelerating the completion of work orders and improving efficiency.
If you wish to save time and stay productive, now is the time to invest in mobile CMMS. NEXGEN offers asset-intensive organizations an intuitive mobile CMMS solution that drives both tangible and non-tangible returns in fast-moving maintenance facilities.