The use of maintenance management systems is increasingly becoming the standard rather than the exception. A recent industry study revealed that 50% of facilities now manage their maintenance-related tasks through a computerized maintenance management system (CMMS). This means that less than half of today’s manufacturing facilities use simple spreadsheets or continue to manage their maintenance using manual processes, such as clipboards and paper files. But even so, CMMS usage isn’t just a trend — it’s a great way for organizations to more effectively practice smart asset management.
Still wondering why should you use a CMMS? The benefits of CMMS software are worth it. A CMMS can help you save time and money, improve health and safety, and much more. For more information, see below.
CMMS Overview
A CMMS, or computerized maintenance management system, is a great way for users to get a handle on their organizations and their overall workflow. CMMS is used to keep track of asset data and maintenance, ensuring that those assets work as intended for as long as possible. This translates to more efficient and transparent operations for organizations that want to make the most of their assets.
If you’re considering adopting a CMMS for your organization, know that you’re making a smart decision. See below for a list of the benefits of using a CMMS.
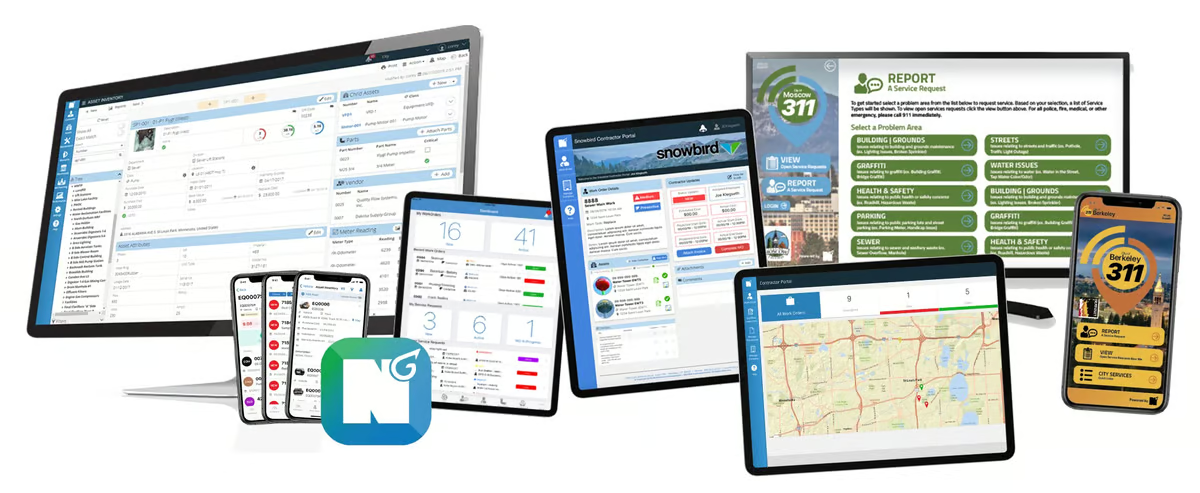
Ready to Learn How CMMS Works?
If you’re looking for a way to make maintenance easier, CMMS software might be just what you need.
What Are the Benefits Of CMMS?
-
A CMMS can unite workflows across different departments of your organization.
Using a CMMS breaks down silos within your organization. Every department can utilise a well-built CMMS, eliminating communication issues and providing a common, shared database with asset information so that every employee is on the same page. This idea is known as EAM (enterprise asset management); it combines the maintenance management functionality of CMMS with asset management and capital planning, ensuring that your organization runs efficiently.
-
A CMMS can save you time, effort, and money.
Ask anyone who has switched to a CMMS – using one saves organizations copious amounts of time, effort, and money. The computerized side of a computerized maintenance management system means that you don’t have to deal with the trials and tribulations of managing work by hand and that everyone in an organization can access the same record database. In addition, using a CMMS ensures that you aren’t practicing reactive maintenance. This means that using a CMMS allows you to preemptively perform scheduled maintenance, thereby avoiding the costly consequences of allowing your assets to run to failure or experience issues such as unexpected or lengthy downtime.
-
A CMMS is useful to a wide number of industries.
Whether you work in wastewater, facilities, or any other industry, a CMMS helps you manage all assets you might be working with. For example, a CMMS can allow a resort to receive service requests from its guests so it can begin scheduling maintenance work, allowing for a convenient way for the resort to keep up with guest communications and resulting maintenance. A CMMS can even help those in the fleet industry to keep track of its maintenance on an individual scale, making sure each vehicle is in top form at any given time.
-
A CMMS can get you detailed reports about your stored data.
A CMMS can not only store and track your organization’s data but can also generate reports about this data. These reports are a convenient way to get a bird’s-eye view of specific information that you might need to further track your data, such as work order costs, or collect information that you need to report for regulatory purposes. In addition, a more advanced CMMS would even allow its users to customize ad hoc reports in addition to using its stock reports, making for a flexible system that allows you to track any data your organization might need.
-
A CMMS can help you keep track of your item inventory.
In addition to housing your service requests, work orders, and others, a CMMS is also capable of storing a detailed database of all of the items in your warehouses and inventory. This means that a CMMS can provide detailed information about what items you have, what items are low in stock, vendor contact information, and more, allowing you to make sure you always have what you need on hand. With its comprehensive item inventory capabilities, handling items with a CMMS is easy.
-
Efficiently Manage Work Requests
The CMMS’s ability to efficiently process all the work requests means saving the largest money and time. Essentially because it permits your employees to submit any requests directly onto the system, helps you set up a priority system for the incoming requests and the CMMS software will then manage them according to the level of urgency. On top of it, a CMMS system enables you to put an end to incoming calls from your project managers because the CMMS software will send regular updates via email. All of your past and current work orders will be easily accessible to you at any time.
-
Organize And Plan Regular Maintenance
The CMMS software provides an efficient method for your Preventive Maintenance department to plan and schedule automated safeguarding activities. Regular maintenance procedures include inspections and pre-emptive repairs. With these preventive maintenance capabilities in your CMMS Software, just imagine how well your equipment and machines will be cared for.
-
Meet Safety And Environmental Regulations
Did somebody say audit? Get rid of printings and tons of paperwork, not to mention unnecessary costs associated with buying printer ink and paper, with your CMMS software. At the same time, the tool will have all the historical data available at the click of a button. This allows your company to meet safety and environmental regulations quickly and easily.
-
Scalability
As your organization expands, so do its maintenance requirements. A CMMS (Computerized Maintenance Management System) is designed to grow with you, adapting effortlessly to increased asset management demands without necessitating a complete system overhaul. This ensures that your maintenance operations can scale seamlessly alongside your business.
-
Flexibility
One of the standout features of a CMMS is its adaptability. Whether you need to adjust maintenance schedules, integrate new assets, or respond to unforeseen challenges, a reliable CMMS can be customized to suit your evolving needs. This makes it an incredibly versatile tool for any organization.
-
Knowledge Retention
A CMMS acts as a centralized repository for all maintenance-related information, ensuring that valuable knowledge is retained over time. This is especially beneficial when there is staff turnover, as the system ensures that critical insights and historical data remain accessible, helping new team members to get up to speed quickly.
-
Enhanced Asset Lifespan
By facilitating proactive maintenance and timely repairs, a CMMS can significantly extend the lifespan of your assets. Instead of waiting for equipment to fail, you can schedule regular check-ups and maintenance tasks, keeping everything running smoothly and saving money on premature replacements.
-
Better Resource Allocation
With real-time insights into maintenance activities and resource usage, a CMMS enables organizations to allocate resources more effectively. You can identify where your team’s efforts are most needed and ensure that materials and personnel are used efficiently, reducing waste and optimizing productivity.
These benefits of CMMS are just the tip of the iceberg. If you’d like to learn more about CMMS features or want to see them in action,